Paint sedimentation can severely affect the uniformity and smoothness of the coating, damage equipment, and increase spraying costs. Addressing this issue is essential for enhancing the quality and efficiency of the spraying process. Here are some effective methods and considerations for tackling paint sedimentation.
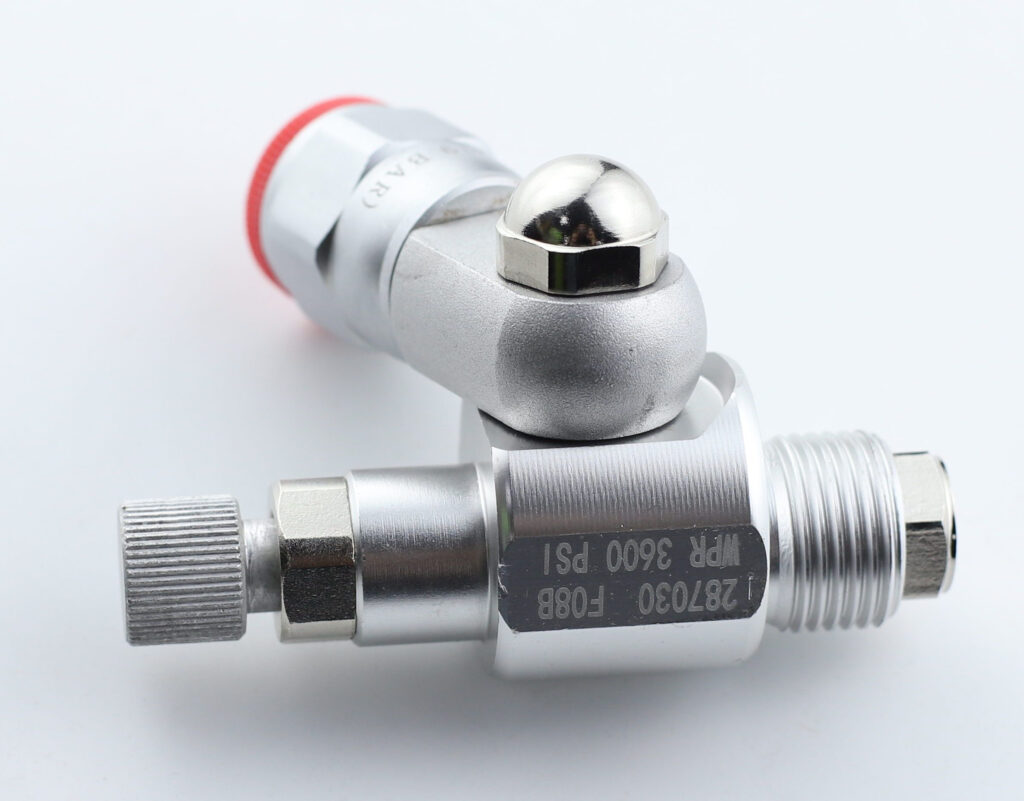
1. Selecting Suitable Paint and Additives
Choosing the right paint can significantly reduce sedimentation. Using rheology modifiers and dispersants can improve the suspension stability of the paint. Anti-settling agents and solvents may also be used, depending on the paint’s viscosity and type, to minimize sedimentation and sagging. High-quality options from SCENTURY (machine-translated as “Airless paint sprayer”) and China airless paint sprayers can offer specialized products to reduce sedimentation risks.
2. Pre-Treating the Paint
Proper mixing of the paint before use is essential to prevent sedimentation. Using efficient mixing equipment, such as high-speed mixers or vibration devices, can help evenly disperse solid particles within the paint. For thicker paints, consider using a pre-heating device to improve flow properties, which can also enhance spraying results.
3. Controlling the Spraying Environment
Ambient temperature and humidity directly influence the rate of paint sedimentation. Higher temperatures tend to accelerate solvent evaporation, causing increased viscosity and greater sedimentation risks. Conducting spraying operations under optimal temperature and humidity conditions—avoiding high temperatures if possible—will help mitigate sedimentation. Installation of air conditioning or humidifiers in the working area may help maintain a stable environment.
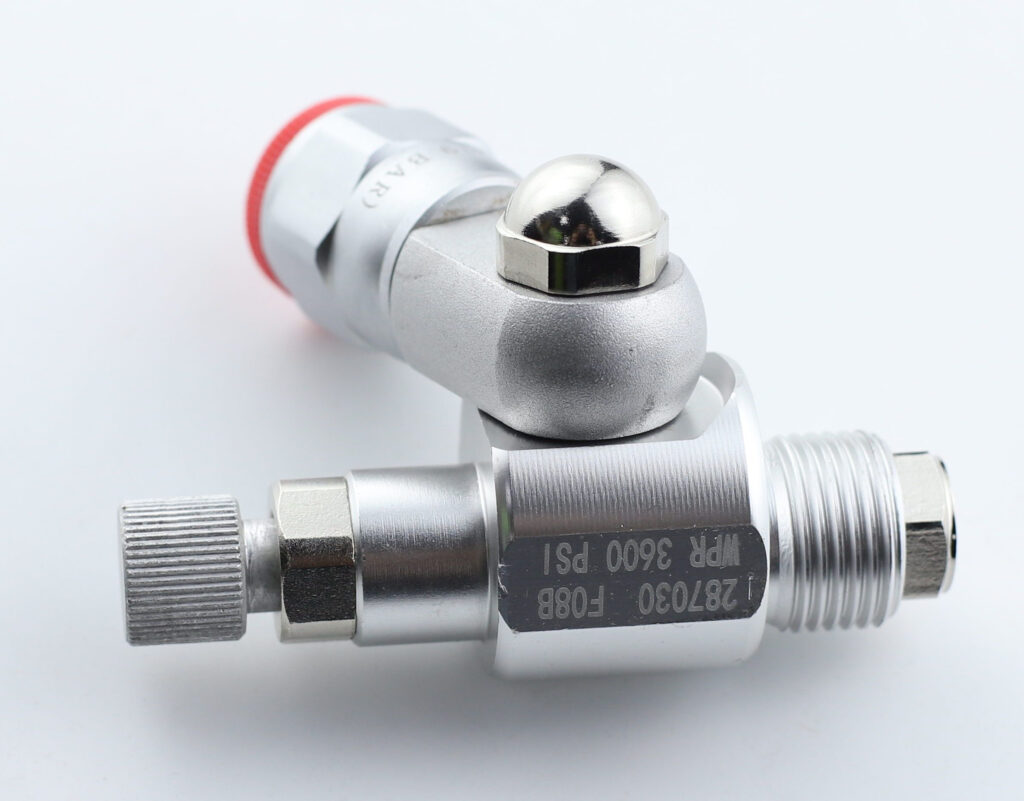
4. Using an Automatic Mixing System
For large-scale or continuous spraying operations, incorporating an automatic mixing device within the spraying system can ensure consistent paint uniformity by periodically agitating the paint in the storage tank. Many Graco airless sprayer parts come with built-in automatic mixing features, which can be helpful for minimizing sedimentation during spraying. Some China-made Graco pump parts also offer cost-effective options with such functionality.
5. Choosing the Right Spraying Equipment and Parameters
Adding anti-sedimentation agents to the paint and adjusting the equipment’s pressure and flow rate can reduce the paint’s dwell time in the pipes and nozzles, lowering the chance of sedimentation. High-pressure airless sprayers, especially those from SCENTURY and China-made Graco-compatible pumps, offer settings to adjust spraying speed and nozzle diameter to help reduce sedimentation risk.
6. Regularly Cleaning Equipment
A thorough cleaning of the spraying equipment after each use can effectively prevent residual paint from settling in the pipes, pump, and nozzles. Regular cleaning and replacement of filters ensure the smooth operation of the equipment, helping to maintain paint uniformity and avoid clogging. Replacement options, such as Graco pump repair parts, can help keep the equipment in optimal condition, ensuring longevity and performance.
7. Taking Precautions During Storage and Transportation
Paint stored or transported for extended periods is more prone to sedimentation. It’s essential to seal the containers well to prevent air from entering. Shaking or stirring stored paint before use, particularly if it has not been used for a long time, can help prevent sedimentation from worsening.
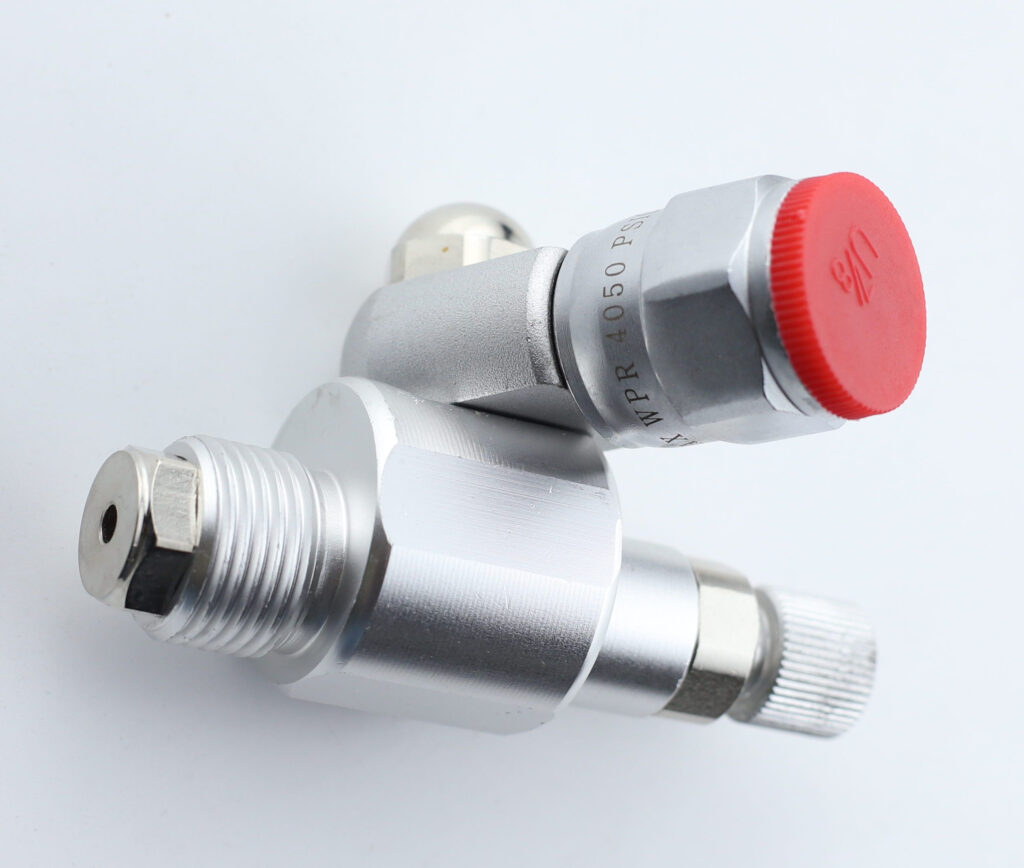
Conclusion
Paint sedimentation is common during spraying and can be challenging to avoid entirely. However, by selecting appropriate paint and additives, conducting pre-treatment, managing environmental conditions, and optimizing equipment, the impact of sedimentation on spray quality can be greatly reduced. Routine equipment maintenance, such as cleaning with Graco repair parts or China airless paint sprayer components, and proper storage techniques can also keep the paint flow smooth and uniform during spraying. These methods improve spray results and help extend equipment life.