In airless spraying, paint clogging is a common and frustrating issue. Clogging can cause nozzle blockages, uneven spray patterns, and even affect the smooth operation and efficiency of the equipment. Solving and preventing clogging issues is essential for maintaining spray quality and improving work efficiency. This article explores the causes of paint clogging and offers solutions, specifically addressing the operation of China airless paint sprayers and Graco airless sprayer parts.
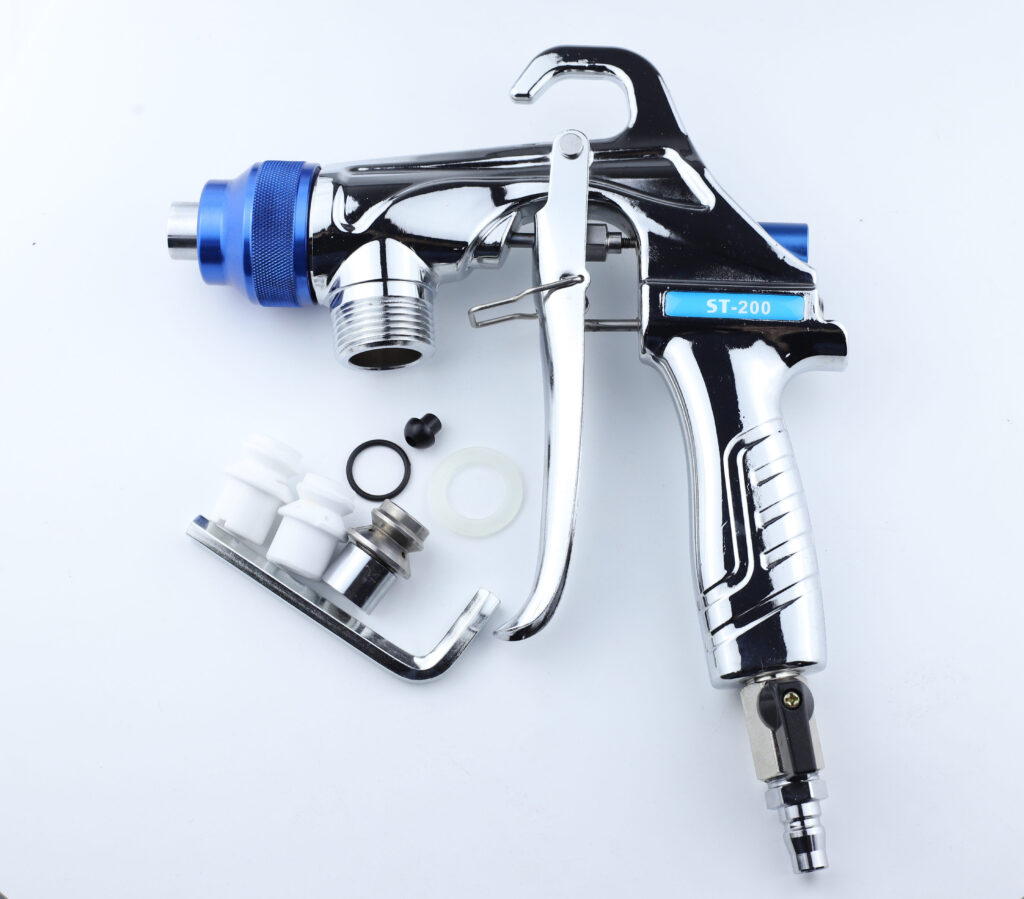
1. Common Causes of Paint Clogging
Unstable Paint Quality Some paints are not stable enough during production, causing sedimentation or clogging after being left unused. This leads to a reduction in paint flow, causing blockages in the spray nozzle. Both China airless paint sprayers and SCENTURY airless paint sprayers may be affected by paint quality.
Insufficient Paint Mixing If the paint is not properly stirred before use, particle clumping may occur, leading to clogging and sedimentation. This can create issues with both Graco airless sprayers and SCENTURY airless paint sprayers.
Improper Temperature Control for Equipment and Environment Temperature affects paint viscosity and flow. In low-temperature environments, paint may thicken and clog more easily. Equipment like Graco airless sprayers may require specific operating temperatures to function optimally.
Ineffective Filtration System A good filtration system is crucial for removing impurities from the paint. If the filtration system is inadequate or the filter becomes blocked, impurities remain in the paint, causing clogs. This is particularly important for Graco pump repair parts and China-made Graco pump parts.
Incomplete Equipment Cleaning Residual paint in the sprayer can mix with fresh paint and cause chemical reactions, leading to clogs. Incomplete cleaning of equipment after each use can lead to clogging and reduce equipment efficiency.
2. Solutions for Paint Clogging Issues
Choose High-Quality Paint Using reliable, stable paint reduces the risk of clogging. When selecting paint, choose options specifically designed for airless sprayers, such as those used in China airless paint sprayers and SCENTURY airless paint sprayers.
Thoroughly Mix Paint Before Use Ensure that the paint is thoroughly mixed, especially if it has been stored for a while. Using an electric mixer can evenly disperse paint particles, reducing clogging risks.
Control Temperature for Spraying Environment and Equipment Select paint and thinners that match the environmental temperature. Avoid spraying in extremely low temperatures, which can lead to paint thickening. If using a Graco airless sprayer or similar model, consider adjusting the equipment’s heating system to maintain optimal paint flow.
Regularly Replace and Clean Filters Ensure that the filtration system is functioning properly. Regularly check for clogged filters and replace them when necessary. Frequent inspection of filters, especially in Graco airless sprayer parts, helps prevent blockages and improves spray consistency.
Keep Equipment Clean After each spray operation, thoroughly clean all parts of the equipment to prevent residual paint from drying and clogging the system. Use appropriate cleaning solutions for critical components, including Graco pump repair parts, hoses, and nozzles.
Add Thinners to Improve Paint Flow If needed, use an appropriate amount of thinner to improve paint flow and reduce clogging. Ensure that the amount used follows the manufacturer’s recommendations for airless paint sprayers.
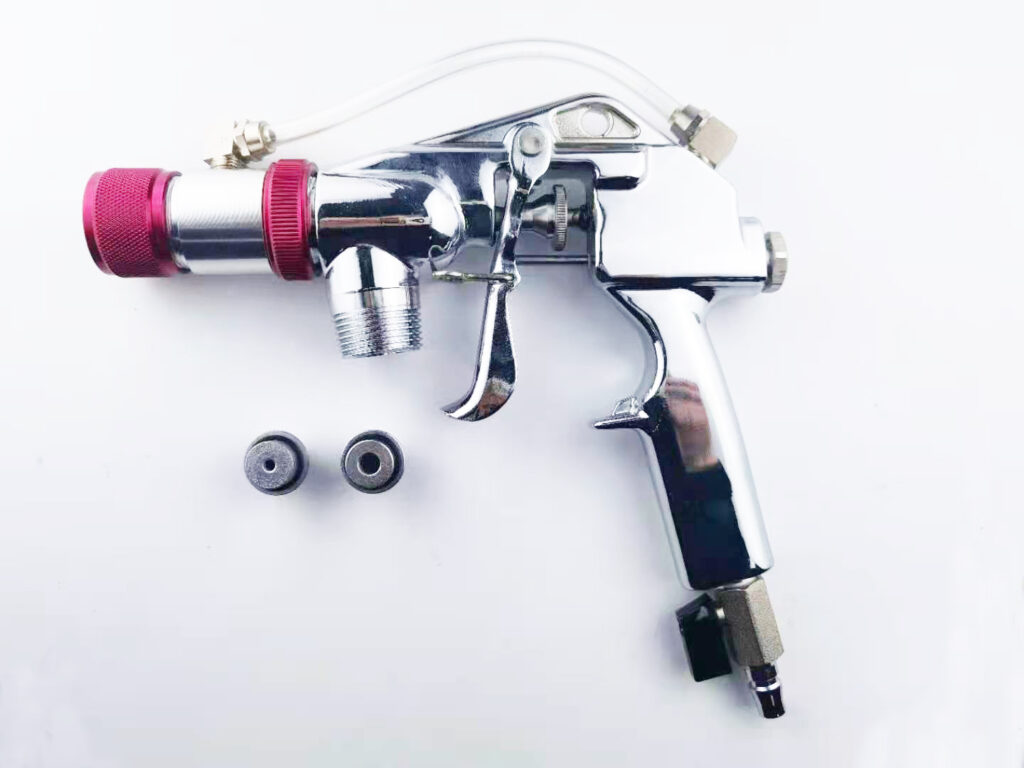
3. Preventative Measures for Avoiding Paint Clogging
Routine Maintenance and Inspection of Equipment Conduct regular maintenance on the airless paint sprayer, focusing on key components such as nozzles, hoses, and filtration systems. This is especially important for Graco airless sprayers and China-made Graco pump parts.
Store Paint Properly Paint should be stored in moderate temperatures and a dry environment. Containers should be sealed tightly to prevent air from affecting the paint. Before use, check the paint for sedimentation or clumping.
Avoid Using Expired Paint Expired paint is more likely to clog due to changes in its composition over time. Always check the expiration date on paint containers and avoid using stored paint that may have deteriorated.
Select the Right Nozzle Choosing the correct nozzle size for your paint viscosity and equipment pressure helps prevent clogging. The right nozzle improves spray uniformity and reduces the risk of clogging, particularly in SCENTURY and Graco airless sprayers.
Operator Training Properly trained operators understand the importance of adjusting spray pressure, selecting the right paint, and cleaning the equipment. This knowledge helps minimize clogging caused by improper handling.
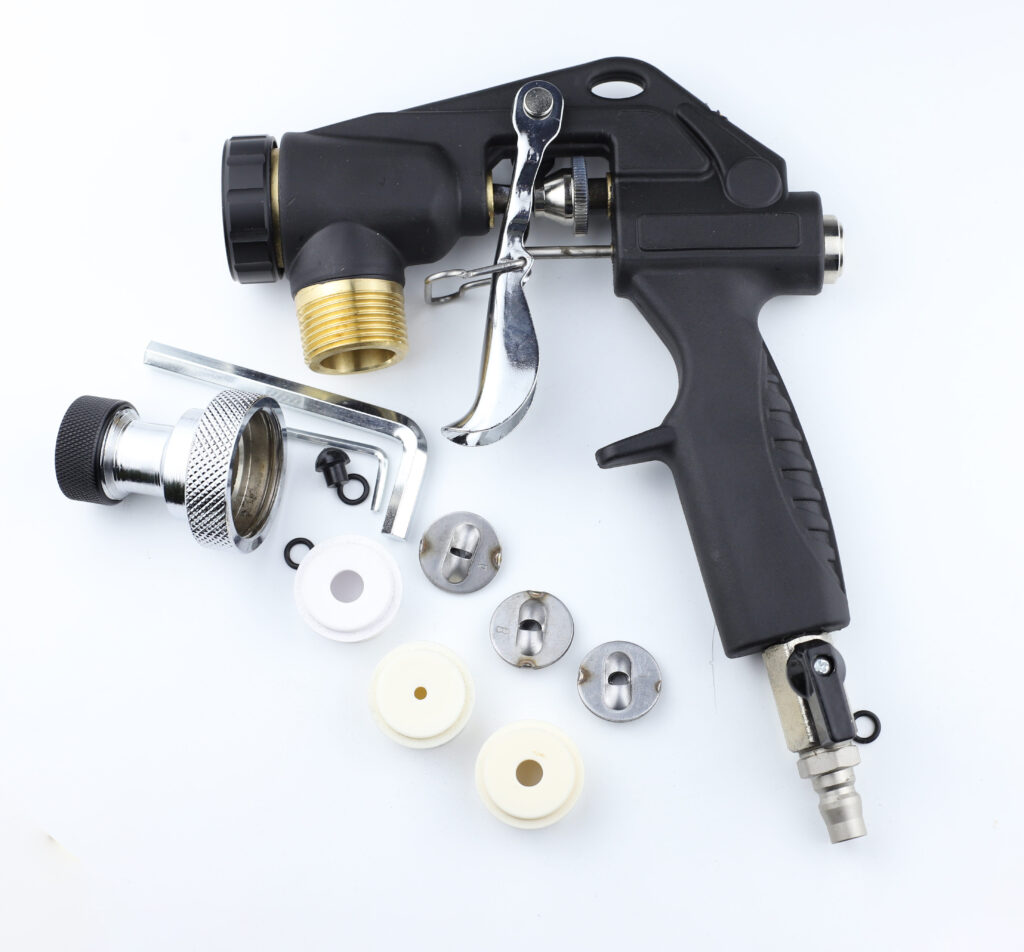
4. Conclusion
Paint clogging can disrupt spray operations and lower quality, especially when working with equipment like Graco airless sprayers or SCENTURY models. Choosing high-quality paint, maintaining suitable storage and mixing practices, regular cleaning and maintenance of the equipment, and maintaining appropriate temperature settings are key to preventing and resolving clogging. These preventative steps help reduce equipment downtime, maintain high-quality spray finishes, and extend the lifespan of essential parts such as Graco pump repair parts and China-made Graco pump parts. Proper handling and care ensure efficient, clog-free operation.